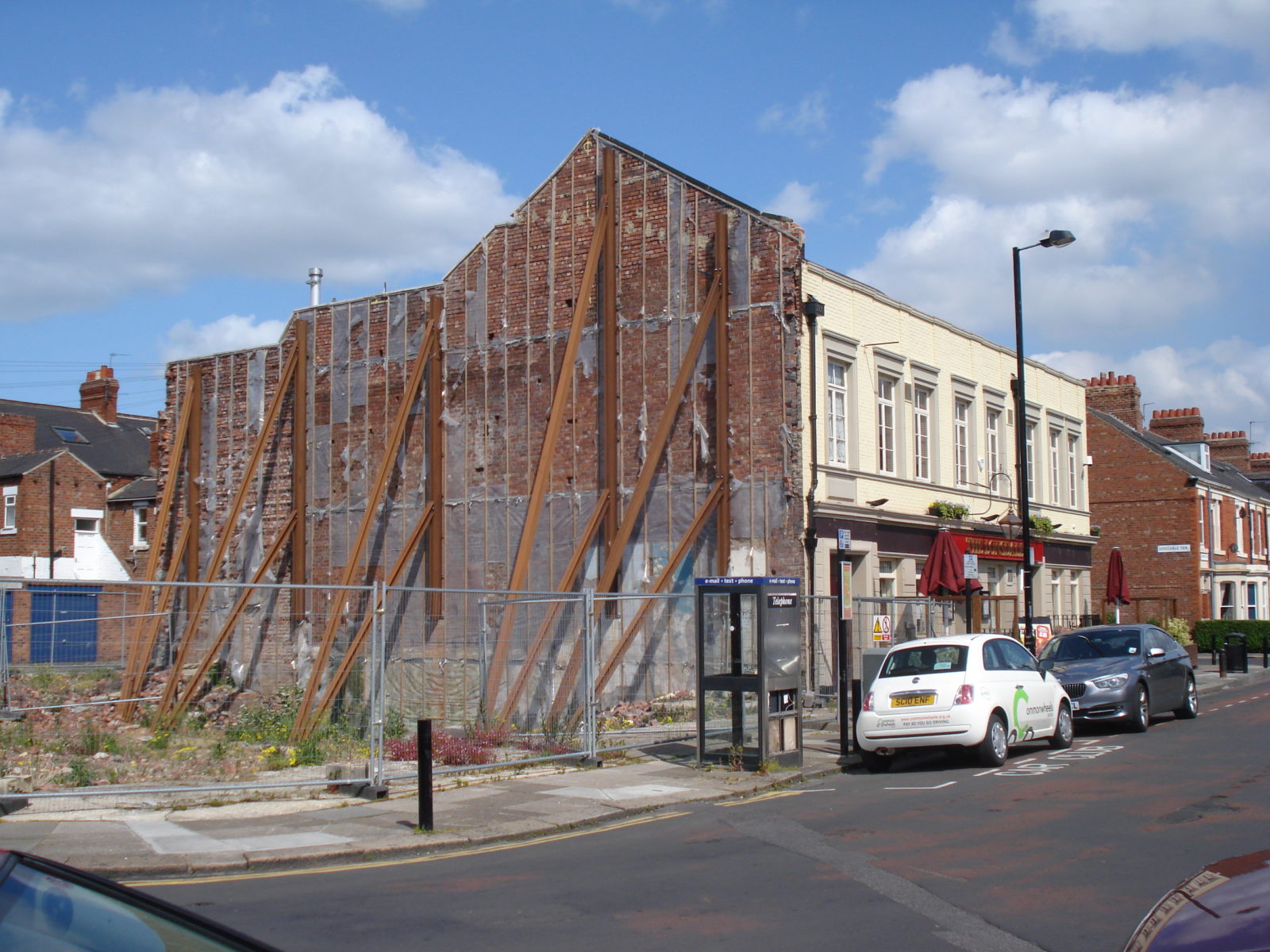
A growing use for Helifix masonry repair and reinforcement systems is to stabilise existing buildings during a new construction phase, enabling major structural works to be undertaken safely and cost-effectively.
There are a wide variety of situations for which Helifix can provide structural stabilisation. Some of the more common temporary requirements are:
- To allow the removal and replacement of significant structural elements
- To reinforce against heavy drilling or piling vibrations
- To allow the creation of new openings and reduce the loadings on other elements
- To open up work space by reducing or eliminating the need for traditional temporary mechanical props
- To reinforce party walls during demolition and development of neighbouring properties
Unlike traditional masonry repairs where Helifix products are installed to provide a permanent structural solution, here, once the construction work is complete the function of the Helifix system is typically superseded. However, the products still remain in place, are fully concealed and continue to provide additional structural support.
The benefits of using Helifix during temporary works are best illustrated through case studies. In the following projects, Helifix engineers have designed solutions that quickly, easily and economically overcome difficult temporary situations which could otherwise have proven dangerous, time consuming and costly to the planned developments.